PET bottle flakes washing line
Product Video:
1000 kg/h HDPE bottles washing line layout
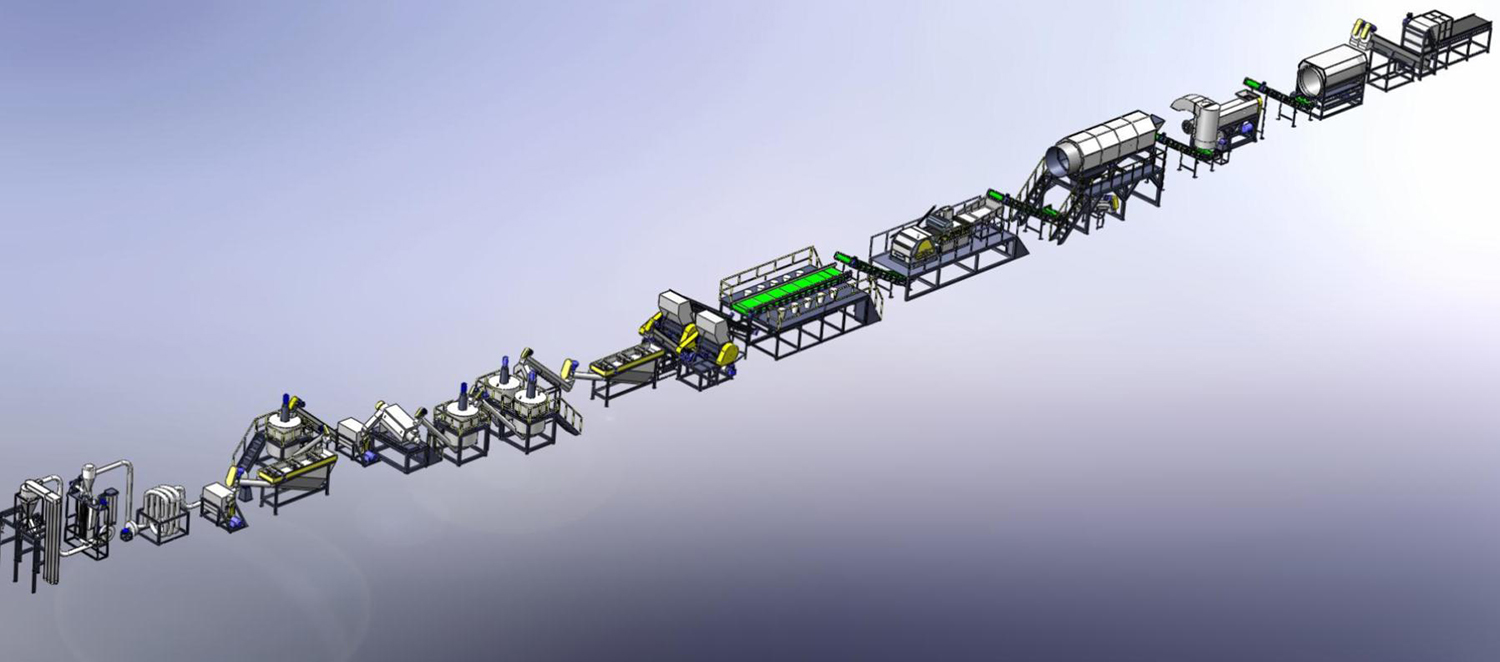
1.Bale opener
2.Belt conveyer
3.Drum screen
4. Belt conveyer
5. Label remover
6. Pre-washer
7.Intelligent optical sorting system
8.Manual sorting system
9.Crusher
10. Hot washer
11.Screw loader
12.Floating washer
13.High speed friction washer
14.Dewatering
15.Round floating washer
16.Floating washer
17.Dewatering
18.Pipe drying
19.Bottle label separator
20.Compacting packing
Features equipment:
1.Bale opener
Newly design PET bottles bales opener. Four shaft effectively open the bales and convey the separated bottles into the belt.
That is more efficient to open the bales and disperse the PET bottles and fully automatic.
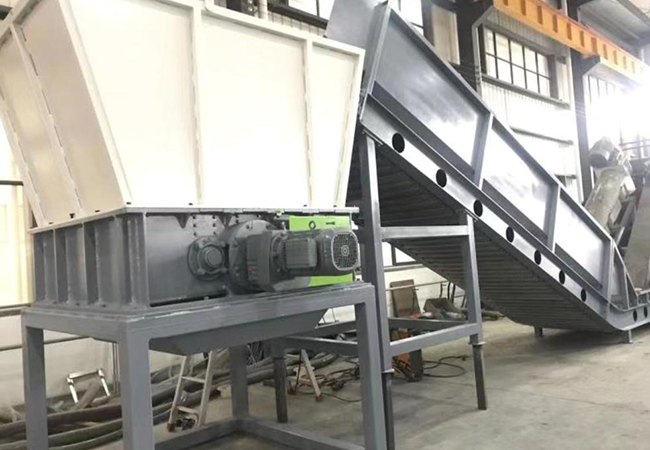
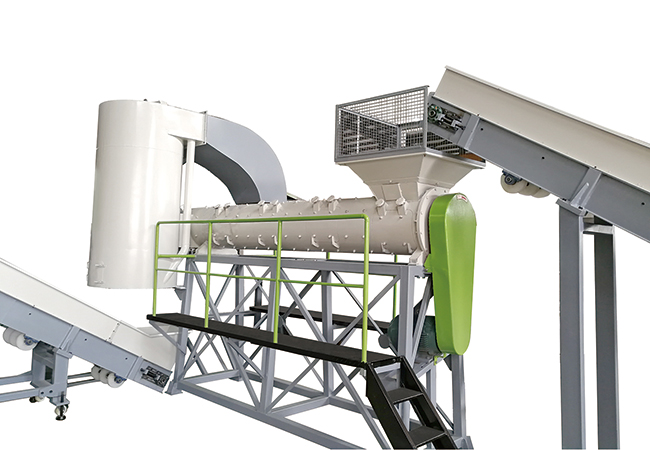
2.Label remover
Effectively remove the labels on the pressed bottles 99% and labels on the round bottles 90%.
It is with the special designed the labels to remove the PET bottles labels. It is highly effective to remove the labels.
3.Dewatering machine
It can remove water and sand to reach moisture 1%.With the NSK bearing, it could have a long time service. The speed is high and dehydrate the moisture and small impurity effectively.
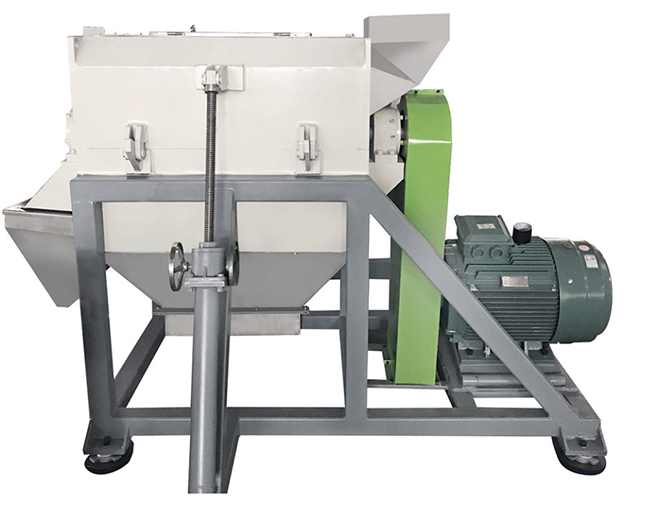
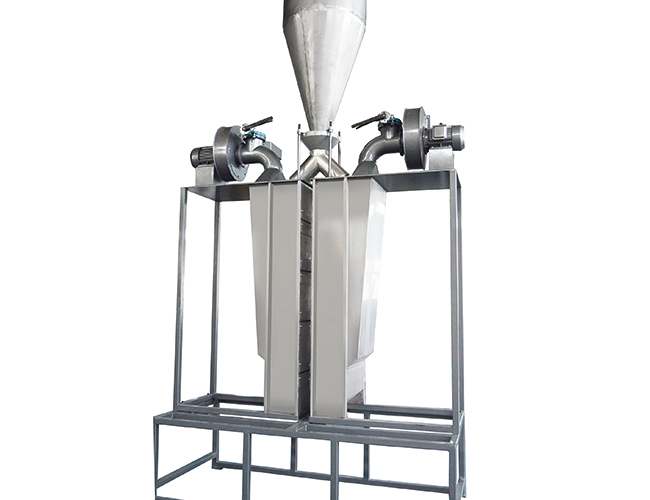
4.Bottle flakes labels separator
Effectively remove the crushed labels mixed in the bottles flakes. With ZIG ZAG design and blower and suction to remove the labels scraps.
The washing line consumption:
Items | Average consumption |
Electricity(kwh) | 170 |
Steam (kg) | 510 |
Washing detergent (kg/ton) | 5 |
Water | 2 |
quality and specification:
Capacity(kg/h) | Power installed(kW) | Required space(M2) | Labour | Steam requirement(kg/h) | Water consumption(M3/h) |
1000 | 490 | 730 | 5 | 510 | 2.1 |
2000 | 680 | 880 | 6 | 790 | 2.9 |
3000 | 890 | 1020 | 7 | 1010 | 3.8 |
flakes quality reference table:
Moisture content | <0.9-1% |
PVC | <49ppmm |
Glue | <10.5ppm |
PP/PE | <19ppm |
Metal | <18ppm |
Label | <19ppm |
Variegated tablets | <28ppm |
PH | Neutral |
Total impurity | <100ppm |
Flakes size | 12,14mm |
A plastic recycling and granulating machine is a type of equipment used to recycle plastic waste into granules or pellets that can be reused in manufacturing new plastic products. The machine typically works by shredding or grinding the plastic waste into small pieces, then melting and extruding it through a die to form pellets or granules.
There are different types of plastic recycling and granulating machines available, including single-screw and twin-screw extruders. Some machines also include additional features such as screens to remove impurities from the plastic waste or cooling systems to ensure the pellets are solidified properly. PET bottle washing machine, PP woven bags washing line
Plastic recycling and granulating machines are commonly used in industries that generate large amounts of plastic waste, such as packaging, automotive, and construction. By recycling plastic waste, these machines help reduce the environmental impact of plastic disposal and conserve resources by reusing materials that would otherwise be discarded.