PET flake granulation machine
The PET characteristic viscosity can be controlled very well without complicated precrystallization dryer system.
PURUI research and design new single screw with compactor especial for processing PET flakes, double cutter and special insulation layer. Adopt underwatering cutting system. The IV drops a little during the whole production process. And the IV can be improved by adding some suitable additives.
new recycling technology is designed for productivity. New force feeding system plus single screw extruder with compactor significantly increased raw material intake efficiency. New type of pelletizing is more user-friendly and low maintenance.
Features & Advantages
High efficient vacuum keeps the IV drop minor
Optimized screw design avoids yellowing
Streamline the process
Pre-drying-free technology saves energy up to 35%
Minimize the investment
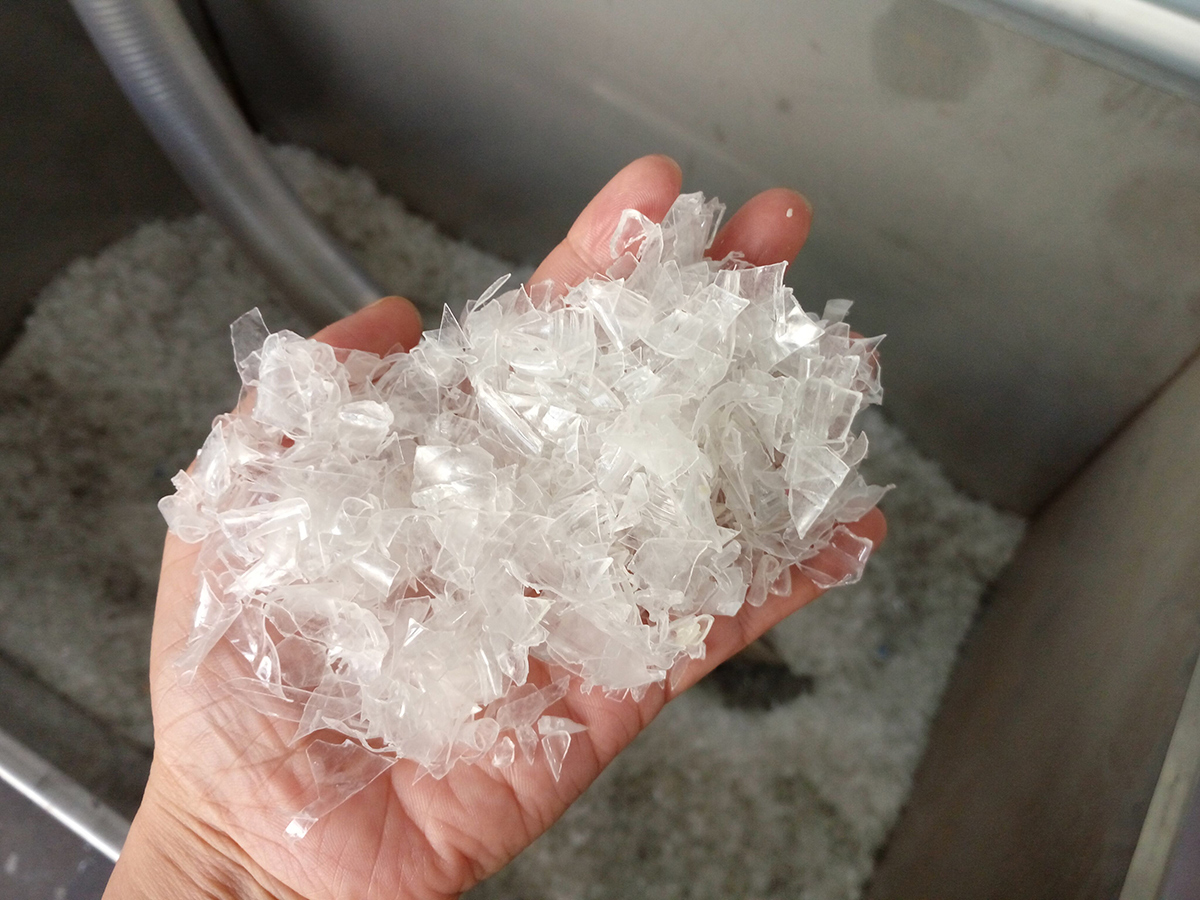
Technical Parameter
Model | Output (kg/hr) |
Screw Speed | Dia. Of Screw (mm) |
L/D | Main Motor power(Kw) | Compactor motor power(Kw) |
CT100 |
300~400 |
400 |
100 |
36 |
90 |
55 |
CT110 |
400-600 |
400 |
130 |
36 |
110 |
75 |
CT130 |
600~800 |
400 |
160 |
36 |
132 |
90 |
CT160 |
800~1000 |
400 |
180 |
36 |
220 |
132 |
Double Layer Disc
Double Layer Disc for excellent degassing
Double disc and mixing dryer, mixing and drying bottle flakes
Instruction: The strong friction and heat generated by the double blade plates cause the material to dry and shrink; the feeding amount is automatically controlled, and there are two sets of temperature monitoring systems.
Blade material: D2 Bi-metal
Steel thickness:8mm

Roots Vacuum Pump
Fast start-up, low power consumption, low operation and maintenance costs, high pumping speed, high efficiency, insensitive to the small amount of water vapor and dust contained in the pumped gas, and a larger pumping rate in the pressure range of 100 to 1 Pa. Can quickly remove the suddenly released gas.
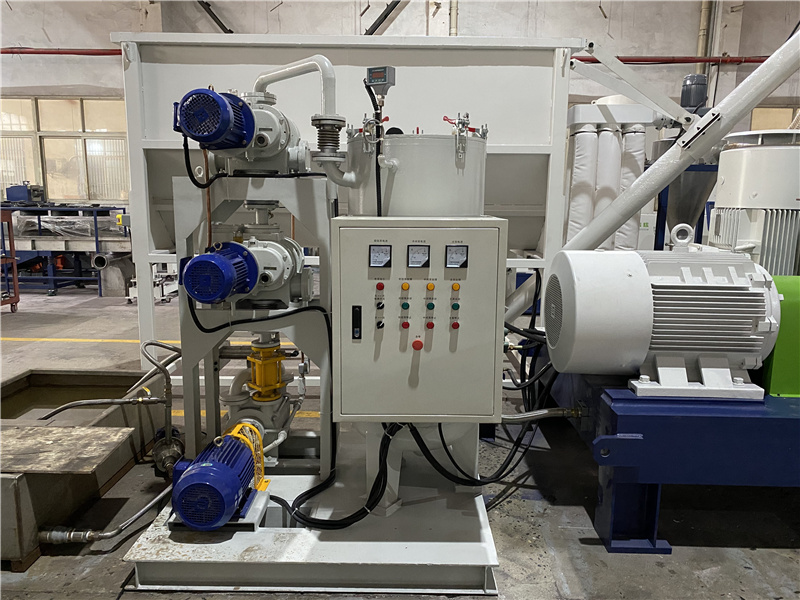
Under water cutting system
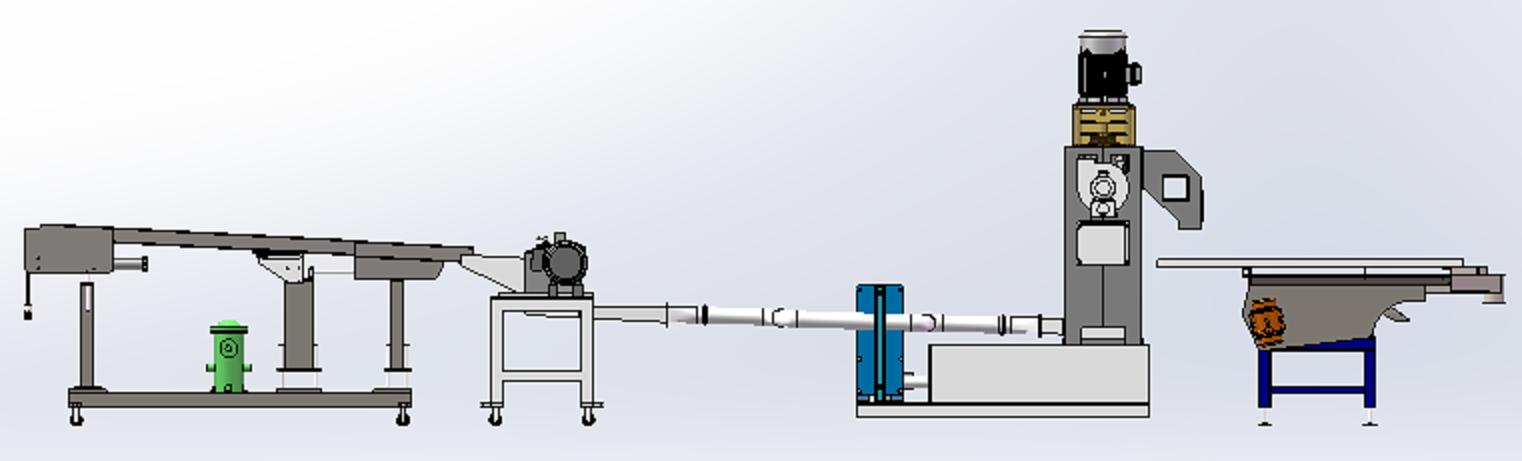
Since the plastic is scraped off by the blade in the melt state and solidified after being cooled by circulating water, the pellets under the melt will not form any dust, and the pellets are of regular shape and uniform size, and the packaging and transportation are more convenient.
The molten plastic is directly cut into pellets after flowing out of the die hole, and is taken away by the cooling water in time. As long as the temperature and flow rate of the circulating water are controlled, the crystallinity of the product can be controlled. The quality of the pellets is very stable, and the transparency and gloss are very stable. Degree is higher.
Since the pelletizing is carried out under water, the oxidation of the product in the air can be avoided.
A plastic recycling and granulating machine is a type of equipment used to recycle plastic waste into granules or pellets that can be reused in manufacturing new plastic products. The machine typically works by shredding or grinding the plastic waste into small pieces, then melting and extruding it through a die to form pellets or granules.
There are different types of plastic recycling and granulating machines available, including single-screw and twin-screw extruders. Some machines also include additional features such as screens to remove impurities from the plastic waste or cooling systems to ensure the pellets are solidified properly. PET bottle washing machine, PP woven bags washing line
Plastic recycling and granulating machines are commonly used in industries that generate large amounts of plastic waste, such as packaging, automotive, and construction. By recycling plastic waste, these machines help reduce the environmental impact of plastic disposal and conserve resources by reusing materials that would otherwise be discarded.